IRIS FACTORY AUTOMATION
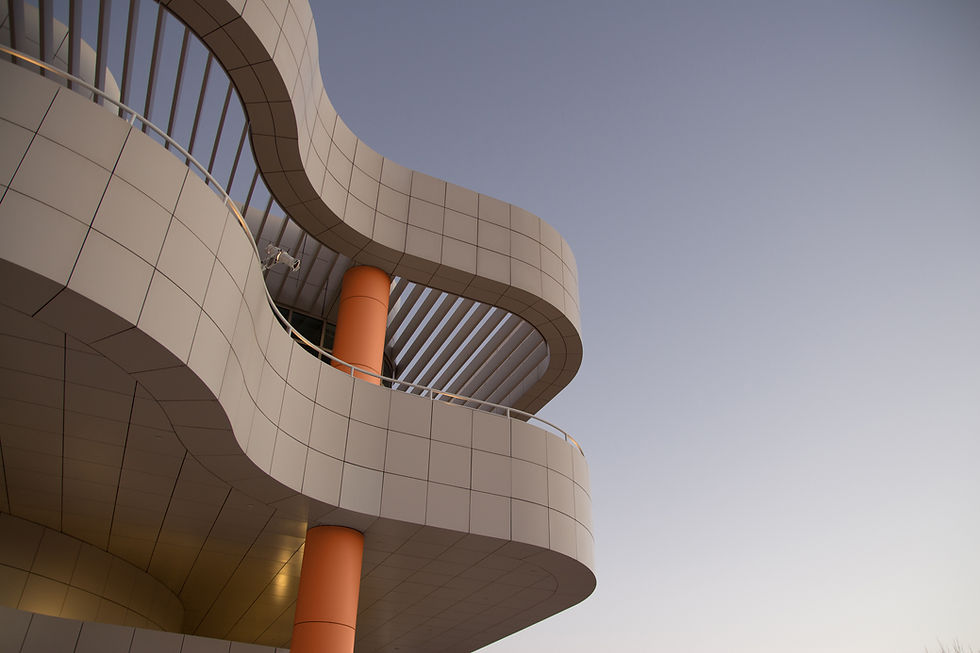
A Comprehensive Guide to Selecting the Optimal Palletizing System for Your Operation
Aug 27, 2024
4 min read
2
54
0
As an engineer familiar with the complexities of factory automation, you understand that the choice of a palletizing system is more than just a matter of capacity and speed—it's about finding the right balance between system capabilities, operational demands, and long-term efficiency. In this guide, we'll delve into the specifics of IRIS's palletizing systems—the RPZ-10, RPZ-20, RPZ-MAX, and RPZ-OPTO—and provide insights on how to evaluate key factors like cycle rates, payloads, and stack heights to ensure you're selecting the most effective solution for your production line.
Key Metrics for Evaluating Palletizers
When choosing a palletizing system, there are a few critical metrics that engineers like yourself should prioritize:
Cycle Rates: The number of cycles a palletizer can execute per minute is crucial, especially in high-throughput environments. A system with a higher cycle rate can significantly increase line efficiency, but it's important to consider whether your operation's upstream and downstream processes can match this speed.
Payload: The maximum weight a palletizer can handle per cycle dictates the range of products it can manage. While payload capacity must align with your product weights, it’s also necessary to factor in the weight of the End-of-Arm Tooling (EoAT), as this reduces the net payload.
Stack Height: Maximizing vertical space is a key efficiency driver, particularly in warehouses with limited floor space. Understanding a palletizer's stack height capabilities ensures you can optimize storage while maintaining pallet stability.
RPZ-10: Collaborative Efficiency for Light Payloads
Stack Height: ~68"
Cycles Per Minute: Up to 7
Payload: 22 lbs (minus EoAT)
The RPZ-10 is a versatile, collaborative palletizer that’s well-suited for operations handling lightweight products. Its collaborative design allows it to function alongside human operators without the need for extensive safety guarding, making it an excellent choice for facilities with limited space or where human interaction with the system is frequent.
Why RPZ-10?
If your operation involves products that don’t exceed 22 lbs per unit, the RPZ-10 offers a balanced solution. Its slower cycle rate is compensated by its collaborative flexibility, allowing for seamless integration into mixed environments where human and robotic workflows intersect.
RPZ-20: Bridging the Gap Between Collaborative and Industrial
Stack Height: ~75"
Cycles Per Minute: Up to 7
Payload: 55 lbs (minus EoAT)
The RPZ-20 is designed for operations requiring a higher payload capacity while still benefiting from the safety and flexibility of a collaborative system. With a payload of up to 55 lbs, it’s ideal for mid-weight products, offering a robust solution without necessitating the full shift to an industrial system.
Why RPZ-20?
For operations that require handling a diverse range of product weights—yet still need the ease of a collaborative system—the RPZ-20 strikes the right balance. Its enhanced stack height and payload capacity make it suitable for more demanding applications while maintaining the advantages of a cobot.
RPZ-MAX: Industrial Strength for High-Throughput Operations
Stack Height: Full Container Height
Cycles Per Minute: Up to 12
Payload: 80 kg (minus EoAT)
The RPZ-MAX is not only engineered for high-throughput industrial-scale production but also designed with safety at the forefront. Capable of handling heavy payloads up to 80 kg and maintaining cycle rates of up to 12 per minute, the RPZ-MAX is built to operate in demanding environments while ensuring the utmost safety. This system is fully compliant with the latest RIA safety standards, making it ideal for environments where the handling of heavy or bulky items poses significant risks. Its robust construction and advanced safety features ensure that even in high-speed, high-volume operations, safety is never compromised.
Why RPZ-MAX?
The RPZ-MAX is the go-to choice for large-scale operations where safety and payload capacity are paramount. Designed to meet rigorous safety standards, this system is perfect for environments that require the handling of heavy loads in potentially hazardous conditions, ensuring your team’s safety while enhancing production efficiency.
RPZ-OPTO: Fully Automated Palletizing with Industrial Precision
Stack Height: Full Container Height
Cycles Per Minute: Up to 12
Payload: 130 kg (minus EoAT)
The RPZ-OPTO offers the same high performance as the RPZ-MAX but with the added advantage of full automation. This system is ideal for operations where consistency and minimal human intervention are critical. The RPZ-OPTO is designed to handle continuous palletizing tasks with precision, ensuring that even the most demanding production schedules are met.
Why RPZ-OPTO?
For facilities aiming to reduce labor costs and increase consistency, the RPZ-OPTO provides a fully automated solution that doesn’t compromise on performance. Its ability to handle heavy payloads at a rapid pace makes it an invaluable asset in any high-volume production line.
Collaborative vs. Industrial: Tailoring Your Choice
As an engineer, you’re aware that the choice between a collaborative (cobot) and an industrial system hinges on more than just capacity. Collaborative systems like the RPZ-10 and RPZ-20 offer flexibility and ease of integration into existing workflows, making them suitable for environments where safety and adaptability are key. On the other hand, industrial systems like the RPZ-MAX and RPZ-OPTO are designed for maximum throughput, handling the heaviest payloads safely, ideal for large-scale operations.
Specialized End-of-Arm Tooling for Optimal Performance
The EoAT is a critical element in maximizing the effectiveness of your palletizing system. For cobots, lightweight and adaptable EoATs are essential to maintain payload capacity and system agility. In contrast, industrial systems require more robust, specialized tooling capable of handling heavier loads without sacrificing speed or precision.
IRIS has developed advanced EoAT options to meet these diverse needs, including the standard SpiderPik end-of-arm tool, which is designed differently for both cobot and industrial lines. The SpiderPik is built with tool-less adjustment capabilities, allowing you to easily reposition the suction cups for optimal placement on various box sizes. This design minimizes downtime and ensures a seamless transition between product sizes, whether you're working with lightweight cobot applications or heavy-duty industrial systems.
Additionally, IRIS offers specialized tooling like side grips for secure handling of large items, multi-zone pick and place configurations, and multi-purpose tools that can accommodate a variety of tasks, further enhancing your palletizing system's efficiency and versatility.
Conclusion
Choosing the right palletizing system is about aligning your operation’s specific needs with the capabilities of the system. Whether you require the flexibility and safety of a collaborative system or the power and speed of an industrial machine, IRIS offers a solution that meets your operational demands. By carefully considering factors like cycle rates, payloads, stack heights, and EoAT compatibility, you can select a palletizing system that not only fits your current needs but also supports future growth and efficiency in your production line.